Cogging, Rubbing and Shorted explained
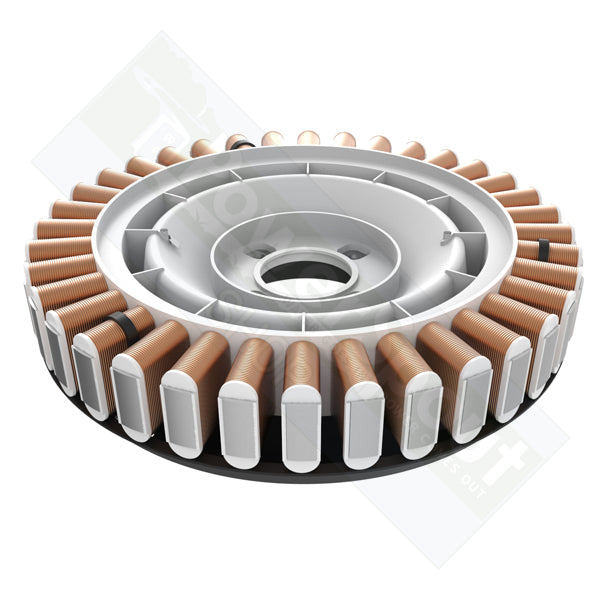
We get a number of queries each month from clients who feel some resistance when they spin the rotor of a turbine's permanent magnet alternator or PMA by hand after unboxing. They may not fully appreciate the difference between cogging, rubbing and shorting. Cogging is normal from new and it does not impact on PowerSpout performance. Rubbing of the rotor on the stator is quite different and should be remedied. A short circuit can also produce similar symptoms. It will not be present in a new PMA, but can occur due to external circuit problems, or internal insulation breakdown after an extended time.
I hope what follows helps to explain the difference and why cogging is bad news for wind turbines but is not an issue for hydro turbines. Some clients, after unboxing it, spin their PowerSpout hydro turbine by hand and notice the cogging toque. They then read online discussions about cogging in the context of wind turbines. They then get themselves very muddled and upset and send the dealer/supplier a long email (and the dealer then contacts me) before they have installed and run the hydro turbine.
Cogging
The stator in the centre of the PMA consists of coils of copper wire that produce the output power. The laminated iron core within this stator provides a low reluctance pathway for the magnetism through the coils, so as to maximise the "flux linkage" effect of the magnets in the outer rotor moving past these coils.
Cogging is the name applied to the condition where magnets on a rotor attract the poles of this iron core in the stator. Think of a set of magnets rotating about a laminated iron core. If the core were smooth, with a uniform surface, there would be no preferred attraction between the core and the magnets. The torque or force needed to turn the magnet drum is always the same (smooth).
Now imagine you have 12 equally spaced magnets and you mill 12 slots in the iron core. The magnets will attract the fingers of the core strongly where it has not been milled, but when the magnet poles are over the slots, the air gap will be large and the magnetic attraction is much less. The two parts will settle at the points where the reluctance (magnetic equivalent of resistance) is least. This is where the magnets are closest to the iron core. When you try and turn it, it needs a larger torque to move the magnet poles away from the iron poles, and then it needs less until you are in line with the slots, and then it tries to overshoot and move in line with the next iron pole. The machine turns in lumps and behaves like a badly cut gear (cog), hence the name cogging. The stators in Smart Drive PMAs (like most others) have prominent poles in the stator cores that result in cogging behaviour as described above.
Cogging is a big problem for small wind turbines, as the static torque prevents the blades from starting to turn in low winds (when they have very little torque). PMAs can be made with no iron core in the stator, and these have several advantages for small wind turbines:
- They are not subject to cogging, so they start easily.
- They also have no "iron loss" so they have better efficiency in commonplace low winds that carry minimal power (but copper losses are high at full power.)
- They do not limit the maximum output current, so it is usually possible to stop a wind turbine even in strong winds, with a short circuit.
Iron cored PMAs use about half the magnets of equivalent ironless PMAs, which helps lower the price, improve the power/weight ratio and the full-power efficiency. The SmartDrive PMAs that we use in PowerSpout turbines are ideal for hydro turbines as they do not have any problem starting, the copper losses are low at full power, and there is no need for short circuit braking.
There are several methods traditionally used to minimize cogging that can be employed in PMAs which include.
Magnets:
- Skewing
- Shaping
Laminations:
- Skewing
- Shaping
These methods intentionally misalign the laminations and magnets. This softens the transitions of the lamination teeth from one magnet to the next and reduces cogging, but it also reduces the PMA’s efficiency because the windings and magnetic fields are no longer optimally aligned.
Cogging does not prevent a hydro turbine from starting because they have plenty of torque, and any detrimental effect of cogging is completely eliminated at the normal running speed of hydro turbines due to their high inertia torque relative to the much smaller cogging torque.
You can feel cogging by turning the PMA rotor by hand. You will feel regular lumps, so it is easy to distinguish from rubbing. Cogging is often confused with rubbing or a shorted PMA.
Note that the cog-free 36-finger-pole Smart Drive PMA we also supply has horseshoe shape magnets and rounded finger laminations. These units have high strength ferrite magnets installed that increase the maximum output power, but slightly reduce the overall efficiency.
The reason this misconception arises is that most people who might pick up a PMA and spin it by hand would naturally conclude that the one that spins freely (without cogging) is more efficient. This is true for wind turbine applications, but not true for our hydro turbines.
Rubbing
Rubbing is where the stator and the rotor touch. This is not normal and is due to a defect.
Rubbing can be caused by:
- Freight impact damage distorting the round components
- Damage caused by dropping the stator or rotor during a service
- Magnetic grit/debris caught in the magnetic rotor
- Failed bearings (where play allows parts to touch)
- Seized bearings, where the shaft has spun and worn the shaft seats (result as above)
- Corrosion under the magnet steel backing which displaces the magnets until they touch the stator (which can occur on very old units running in wet conditions)
In order to check for a rub, remove the rotor and chalk a line on the magnets. Then put the rotor back on and spin it by hand, if the chalk rubs off the rotor and onto the stator you have a rub.
A rub will also feel different, but as a rub and cogging are often combined it can be difficult to feel a light rub, hence the need to use chalk. A rub is a constant drag whereas a cog is a lumpy regular motion.
If the turbine has been running for some time, a rub is easy to spot at a service check, as the point of the rub will have been polished by the repeated contact.
Shorting
A short circuit between any two of the three phases will result in a braking action that feels similar to a severe rub when turned slowly by hand. A short is a drag and does not have the lumpy feel of cogging.
A shorted PMA will likely be hotter to the touch than normal, just after it has been stopped.
When operating the Watts will have decreased significantly, and the RPM will have increased which you will hear as increased noise.
Remember a short is more likely external to the PMA, for example in the:
- Rectifier
- DC cabling from the rectifier
- Connected electronic equipment after the rectifier
If you suspect a shorted PMA, you should start by disconnecting it from the rectifier, then spin it at constant speed with a battery drill and check that the AC line to line voltages (between each phase) are all about the same. If they are your PMA is not internally shorted. If you have an internal short (partial short or broken wire) you will measure one lower line to line voltage than the other two. If it spins freely with equal voltages then check the rectifier with a multimeter and examine the wiring for external short circuits.